What Is Thermal Mapping And The Importance Of Thermal Mapping In A Cold Chain Management. Unlocking The Potential Of Artificial Intelligence In A Cold Chain
Thermal mapping is part of Good Manufacturing Practice (GMP), It was created to assist life-science businesses in keeping an environment’s boundaries under surveillance. This procedure is designed to stop temperature and humidity fluctuations in a controlled environment, such as a warehouse, storage, container or vehicle.
Below is the definition from MHRA inspectorate on the aspect of the thermal mapping in the storage area.
Mapping is crucial to “demonstrate by way of documented evidence that the chosen storage area is suitable for the storage of temperature-sensitive medicinal products. Ambient products are also temperature sensitive. A mapping exercise of the proposed storage area will ensure that the company will understand their storage area and identify any potential areas therein that may be unsuitable to store medicines. A mapping exercise will also inform as to where permanent thermometers should be located.”
Temperature, humidity, and air quality are factors with significant influence on the status of the final product, consequently on the release or rejection of produced batches. Hence, all recommended good practices such as GMP, GCP, GDP, GSP, GPP, etc. must be well implemented or applied to have the right medicine that is safe at the right place from the right person (professional) to the real beneficiaries/patients.
Thermal mapping is described as the process of predicting an unknown temperature at a given point and further generating a profile based on multiple points within the given specified space. Thermal mapping provides easy identification of the hotspots in the specified space.
Data loggers and Building Management System (BMS) probes are the most common devices/sensors that are used by many companies to trace and track the products temperature profiles. BMS’s main function is to control internal environment conditions through automation. The tracing systems have to operate independently of the refrigeration systems to ensure that if anything goes wrong with the refrigeration system, the tracing system has to remain operational. Data Loggers are portable devices and can be easily installed or attached to a pallet, or container in a variety of modes of transportation.
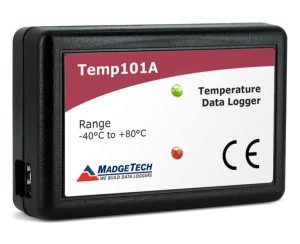
Picture of the Data Logger used by BPV engineers on client sites
Pharmaceutical products must be reliably traceable throughout their entire life cycle, which requires monitoring of the cold chain in the industry.
Cold Chain is a division of the logistics sector which links the production, storage and distribution, and use of chilled pharmaceuticals for the diagnosis, treatment, and prevention of disease.
Cold Chain Management:
- The cold chain is critical for maintaining product integrity during transportation and storage, i.e., penicillin V oral solution, after being reconstituted with water, it becomes susceptible to degradation by hydrolysis and should be stored in a refrigerator and used within 7 days. If not refrigerated, as much as 10% of the active ingredient will degrade within 24 hours. Preservatives such as sodium benzoate may be included in the formulation.
- The temperature of different spaces within cooling rooms, industrial fridges and other controlled temperature environments can vary by up to 10°C. Typically, the central space within a chamber will maintain the most constant temperature, while the corners and areas surrounding the fans and access points will fluctuate. There is also external seasonal weather influence to consider, especially in warehouses
- Maintaining the cold chain during distribution requires a good understanding of product stability, mode of transportation, ambient temperatures during transportation, performance of packing solution and time needed to reach the destination.
The main disadvantages of current cold chain systems are a lack of overall planning and coordination of upstream and downstream activities and a low level of cold chain logistics technology. Each party in the cold chain operates independently of the others and manages its own finance independently. This leads to inefficiency and an inability to control an entire supply chain from the pre-production phase to the patients stage.
Beginning of AI technology and Future Possibilities To Be Utilised in Cold Chain Management
Fortunately, we are the witnesses of advanced technology improvements in terms of AI and its potential adoption in the life-science industry. Tools and systems based on blockchain, cloud storage, and the Internet of Things (IoT) are the main drivers of change.
Blockchain is a safe distributed ledger that enables trusted transactions between untrusted parties.
The Internet of Things can be the perfect platform for tracking the status of goods in the cold chain in real-time. In order to realize intelligent object recognition, positioning, and other functions. The Internet of Things (IoT) connects objects through different networks and transmits information and data exchange between IP addresses. Real-time access to information about physical objects is made available.
Pharmaceutical products must be reliably traceable throughout their entire life cycle, which requires monitoring of the cold chain in the industry. In addition, each cycle can be tracked by an independent ID such as a barcode which travels with the product through the entire journey up to the customer. All these components can be linked to separate cloud storage with safety protocols and cannot be tampered with. This would provide traction in real-time and traceability at every stage of the cold chain management, in addition to evaluation of the data in terms of the temperature of the storage and humidity, etc in order to reduce overall costs per product.
In the pharmaceutical sector, it is crucial to guarantee product efficacy. Throughout every stage of a pharmaceutical product’s life cycle, from production to distribution and storage, temperature management is essential for preserving its integrity.
Liquid pharmaceutical products such as solutions, solutions for injection, and solutions for infusions are essential in the treatment and diagnosis of disease, but they also consume most of the budget. They must be managed carefully to avoid resource waste and the loss of lives due to inadequate quality or poor management in relation to the advised good practices.
Good Storage Practices (GSP) are essential for the management of quality pharmaceutical products throughout the whole health commodities supply chain. When applied correctly, the assurance increases that stored pharmaceutical products are safe and of excellent quality.
++++
Please stay tuned, we are going to publish the next article about thermal mapping and the importance of seasonal temperature mapping in summer and winter.