Understanding Equipment Used in Temperature Mapping: Thermocouples, RTDs, pt100 sensors and Data Loggers
In pharmaceutical manufacturing, precise temperature detection and documentation are essential for the validation of temperature-sensitive processes and products using temperature mapping. Examples of temperature-sensitive processes include sterilisation, freeze drying, depyrogenation, and the storage of medicines with precise storage conditions. Thermocouples, RTD’s, PT100 sensors and data loggers are examples of equipment used in achieving this aim. This article aims to explain these sensors and answer frequently asked questions when selecting appropriate temperature probes to monitor and validate processes.
What are thermocouples?
Thermocouples are a type of temperature sensor made up of two different conducting metals or metal alloys joined at one end. Thermocouples work on the principle of the thermoelectric effect, which means that under the same conditions, a different voltage is generated in each wire due to the properties of each metal. The voltage difference between these two wires is proportional to temperature and this relationship is well documented for numerous thermocouple types, allowing the temperature of the surrounding environment to be detected with a high degree of accuracy.
What types of thermocouples exist and why?
There are ten different types of thermocouples detailed in IEC 60584-1, which is the international standard for thermocouples. These are thermocouple types R, S, B, J, T, E, K, N, C and A. The metals making up each thermocouple type are detailed in the table below. Each type of thermocouple has a different temperature range and environmental constraints. The diameter of the wires also plays a role in determining the temperature range. It is advisable to consult the thermocouple manufacturer’s documentation to verify the temperature range and environmental constraints, ensuring the thermocouple is suitable for the intended temperature mapping application.
Thermocouple Type | Positive conductor | Negative Conductor |
R | Platinum- 13% rhodium | Platinum |
S | Platinum- 10% rhodium | Platinum |
B | Platinum- 30% rhodium | Platinum – 6 % rhodium |
J | Iron | Copper-nickel |
T | Copper | Copper-nickel |
E | Nickel- Chromium | Copper-nickel |
K | Nickel- Chromium | Nickel – aluminium |
N | Nickel- Chromium- Silicon | Nickel – silicon |
C | Tungsten – 5 % rhenium | Tungsten – 26 % rhenium |
A | Tungsten – 5 % rhenium | Tungsten – 20 % rhenium |
What is important to consider when choosing thermocouples?
- Thermocouple specification by country/ region. For example in the UK guidance is available in BS 54937:1993, in Europe it is set out in BS EN60584-3:2003 and in America, this is available in ANSI MC96.1.
- Wire thickness: Thinner wires are more responsive, but are more fragile and more difficult to work with.
- Encapsulation: Thermocouples can be encapsulated with a range of materials such as Teflon and stainless steel either fully, partially or not at all. Thermocouple encapsulation extends the life of the thermocouples but it can slow response time so decisions should be made based on the intended application.
- Temperature range: Each thermocouple type has different properties which make them more suitable to being used in certain temperatures. It is critical that the thermocouple type used is capable of accurately operating at the desired temperature.
What are RTD’s?
RTD stands for Resistance Temperature Detector and these sensors are used to monitor and validate manufacturing processes. RTDs contain a resistor whereby the resistance changes with temperature. A common type of RTD is a 100-ohm platinum wire wound around a core material and covered with some type of sheath.
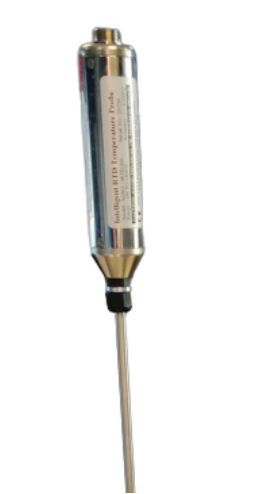
What are the main differences between RTDs and Thermocouples?
RTDs offer greater accuracy and repeatability than thermocouples, making them ideal for pharmaceutical process monitoring, such as measuring temperatures at specific points in a freeze dryer, including the condenser and drain lines. They may also be preferable for measuring product temperature, as they average the temperature over the entire sensing element, whereas thermocouples provide a point measurement at the junction of their two wires. The smaller the RTD sensing element, the closer its measurement will be to a thermocouple’s point measurement. However, thermocouples have their advantages, including a wider temperature range and lower cost.
What are PT100 sensors?
PT100 sensors are a common type of RTD. The PT denotes the chemical symbol of the metal used (platinum) and the 100 denotes the resistance of the device at 0 °C. There may be one or more sensing resistors within a protective sheath with internal connecting wires and external terminals to allow the connection of electrical measurement instruments.
What is the difference between PT100 sensors and thermocouples?
PT100 sensors are a type of Resistance Temperature Detector (RTD) and work via a different mechanism (please see section above).
T100 sensors and thermocouples are both used for temperature measurement, but they operate on different principles and have distinct characteristics:
- Principle of Operation:
- PT100 Sensors: These are Resistance Temperature Detectors (RTDs) that measure temperature by correlating the resistance of the platinum element with temperature.
- Thermocouples: These measure temperature based on the Seebeck effect, where a voltage is generated at the junction of two different metals when there is a temperature difference.
- Temperature Range:
- PT100 Sensors: Typically used for temperatures ranging from -200°C to 850°C.
- Thermocouples: Can measure a wider range of temperatures, from -200°C to 1750°C, depending on the type (e.g., Type K, Type J).
- Accuracy:
- PT100 Sensors: Generally more accurate and stable over time.
- Thermocouples: Less accurate compared to PT100 sensors but sufficient for many industrial applications.
- Response Time:
- PT100 Sensors: Slower response time due to the thermal mass of the sensor.
- Thermocouples: Faster response time, making them suitable for applications requiring quick temperature changes.
- Signal Type:
- PT100 Sensors: Provide a resistance output that needs to be converted to temperature using a calibration curve.
- Thermocouples: Generate a millivolt signal that corresponds to the temperature difference between the junctions.
- Durability:
- PT100 Sensors: Generally more robust and less prone to drift over time.
- Thermocouples: Can be more susceptible to drift and degradation, especially at high temperatures.
- Cost:
- Thermocouples: Inexpensive, especially when bought in bulk. The price can vary depending on the type but they are generally cheaper than PT100 sensors.
- PT100: Generally more expensive than thermocouples.
What are Data Loggers?
A data logger is an electronic device that records and stores data at defined intervals so that it can be retrieved at a later date. They can be used in a wide range of temperature mapping applications and can be designed to sense other variables such as humidity and pressure. Data loggers are commonly made up of two components, a sensor and a digital processor, which enables the data to be collected at defined time points and stored. When measuring temperature, the sensor used can be based on either a thermocouple or resistance-based detector, see the above paragraphs for more details.
An example of a data logger used for measuring environments between -40 °C to +80 °C
What is important to consider when weighing up whether to use thermocouples or data loggers in your study?
- Cost
Thermocouples: Inexpensive compared to dataloggers.
Dataloggers: More expensive, but can save time, which can lead to shorter project timelines.
- Set up time:
Thermocouples: Can be more fiddly to insert, and you need to allow additional time for this in your project. For example, when using thermocouples for autoclaves, they have to be fed through an entry gland at the back.
Data Loggers: Generally easier and quicker to use, which can shorten project timelines.
- Calibration requirements:
Thermocouples: Thermocouples have to be calibrated at the start of each validation project and can drift over time which can mean you either need to recalibrate if the TCs are in situ for extended periods, or sensors may fail post calibration which could void data.
Data Loggers: Dataloggers are usually calibrated on an annual basis. If they fail calibration verification (which can happen) you have to review all the tests they have been used for to check if that calibration drift has impacted any studies.
- Response time:
Thermocouples: Faster response time which may be beneficial for some applications, such as autoclaves where BS EN285:2015 states that sensors should have a “response time in water of 𝜏 90=0.5”.
Dataloggers: Generally slower response time, but it is important to consider if the response time of your data logger meets the desired application as it can be overkill for certain applications.
- Steam Path (for autoclave applications):
Thermocouples: For placing thermocouples inside of loads such bags, effort must be made to make sure the bag can be successfully sealed at the point of thermocouple entry, as this can affect the steam path. In cases where bags have not been correctly sealed, this has led to false passes in validation studies as leaving a bigger gap allowed more steam in to sterilise the item, which wasn’t a true representation of the real life operation.
Data loggers: Can be fully sealed within autoclave bags without obstructing the steam path.
What is important to evaluate when looking at temperature sensors for pharmaceutical applications?
Environmental conditions
It is important to consider the environment in which the sensors will be used during temperature mapping. For example, what is the operating temperature range that they need to work under? How will the size of the logger used impact its ability to be placed in the desired location? Are there any environmental factors such as being in an explosive or high humidity environment? How durable are the sensors likely to be over time with repeated use in your desired environment? These are all factors that may influence what type of sensor will be best for the specific environment. For example, in fridge freezer temperature mapping, you may choose to use data loggers because they are easy to place and work within the temperature range you want. In another situation, where you need to evaluate the temperature changes inside an autoclave, you may choose to use thermocouples, because their flexibility and their ability to be used in hard-to-reach locations and work across a wide range of temperature and pressure , making them versatile for various industrial environments.
Resolution
Sensor resolution refers to the smallest possible change that a sensor can perceive. A higher resolution allows for more precise measurements, allowing engineers to detect smaller changes in the input stimulus.
Response time
Response time is the time at which a sensor is able to read the temperature difference of the surrounding environment. In other words, sensors take time to ‘warm up’ and start taking accurate measurements. It is usually written as 𝜏 (n)= time, using the Greek constant, 𝜏 (tau) plus a number with a number afterwards which indicates the percentage of the temperature difference to be measured. For example, 𝜏 90 indicates the time taken for 90% of the temperature difference to be measured. Response metrics are determined by sensor size, housing thermal mass and the surrounding environment because all of these factors influence the heat transfer rate. As a general rule, smaller sensors will have a faster response time than larger sensors because of the faster heat transfer rate. Typically sensors with a faster response time cost more and faster response times are not needed for all applications.
For some applications, response time is highly relevant, such in validating autoclaves in which BSEN285:2015 recommendations state that sensors should have a “response time in water of 𝜏 90=0.5”. This is a big discussion topic at the moment because current dataloggers on the market are unable to meet this, only thermocouples.
Calibration and validation
Temperature probes must be regularly calibrated and must be validated in order to ensure accurate and reliable measurements. Without routine calibration, sensors may drift over time and give off false temperature readings, which puts temperature-sensitive pharmaceutical products at risk. To ensure the probe’s accuracy, calibration entails comparing the probe’s readings with a reference standard. Validation, on the other hand, demonstrates that the probe continuously operates within reasonable parameters. Both calibration and validation are essential for pharmaceutical products to be of the highest quality and safety, in addition to complying with regulatory requirements.
Stringent accuracy and precision specifications are required for probes used in critical process monitoring points, typically ±0.1°C or better. It is best practice to ensure that the calibration laboratory is accredited or traceable to ISO/IEC 17025 standards, which demonstrates a laboratories ability to operate competently and generate valid results. In the UK, the recognised accreditation body for ensuring ISO/IEC 17025 compliance is UKCAS.
During calibration sensors can be tested at two or three different temperatures (“2 or 3 point calibration”) that cover the entire temperature range that the sensor is expected to monitor. The highest level of accuracy assurance at every point in the range is provided by “3 point calibration,” which is required in departments operating under an MHRA license.
Conclusion
In conclusion, temperature probes used in pharmaceutical applications must be highly accurate and precise, as well as robust and responsive. The variety of features that support data integrity and accessibility, as well as validation and documentation simplicity, are benefits. Choosing the right probe technology and design for the specific process’s purpose and circumstances allows for reliable monitoring and control.
Further Reading
Martin Rowe for EDN. “Thermocouples: Simple but misunderstood”
https://www.edn.com/thermocouples-simple-but-misunderstood
MHRA. “GxP Data Integrity Guidance and Definitions.” 2022. https://www.gov.uk/government/publications/gxpd-data-integrity-guidance-and-definitions/gxpd-data-integrity-guidance-and-definitions
Rogers, G. “Calibration and Traceability in Pharmaceutical Manufacturing.” Dublin Institute of Technology, 2020. https://arrow.tudublin.ie/sciendoc/246/
Williams, L. (2018). Temperature Control in Pharmaceutical Manufacturing. [Doctoral Dissertation]. University of Manchester.
Nail, S., Tchessalov, S., Shalaev, E., Ganguly, A., Renzi, E., Dimarco, F., Wegiel, L., Ferris, S., Kessler, W., Pikal, M. and Sacha, G., 2017. Recommended best practices for process monitoring instrumentation in pharmaceutical freeze drying—2017. Aaps Pharmscitech, 18, pp.2379-2393.