Installation Qualification (IQ) and Operational Qualification (OQ) are essential for new porous load autoclaves in the pharmaceutical and medical device manufacturing industries and forms a vital component of Good Manufacturing Practices. Some of the IQ/ OQ tests can be conducted as part of Factory Acceptance Testing (FAT) and Site Acceptance Testing (SAT) so it is good practice to create a document called a ‘Requirements Traceability Matrix’ which outlines each of the testing criteria required and when and where it is going to be conducted.
This article will be an accumulation of our knowledge of best practices in the industry for both IQ and OQ, with reference to BS EN285:2015 as this is a British Standard that is commonly followed in the industry containing all methodologies behind the technical tests described, in addition to acceptance criteria.
What are Installation Qualification (IQ) Tests for porous load autoclaves?
Installation Qualification tests for autoclaves are designed to verify that the autoclave as installed or modified, complies with the approved design and manufacturer’s recommendations. Tests must ensure that the autoclave is installed and constructed correctly, all documentation is in place. These elements can be assessed and recorded as part of an approved Installation Qualification Protocol.
For documentation, it is necessary to confirm:
- Calibration Certificates are present and in date for the autoclave itself
- Applicable certifications (CE marks etc.) are present and in date
- The correct installation of components, equipment and pipework against P&ID (piping and instrumentation diagrams)
- The presence of Operating and Engineering Manuals
- Weld logs are present
- Wiring Checks have been carried out
- Recoding of software and firmware versions.
Installation Checks involve verifying:
- Materials of construction
- Dimensions
- Operational ranges (temperature, humidity, CO2 etc.)
- Number of shelves/ drawers
- Utility connections
- Environmental and Location Suitability
What are Operational Qualification Tests for porous load autoclaves?
Operational Qualification (OQ) is essential to verify the autoclave’s ability to perform as intended throughout the anticipated operating ranges. Tests are executed without the product to ensure the system operates as designed. During this stage, safety switches, alarms and upper and lower operating limits will be confirmed. Operational Qualification involves a series of initial checks on the documentation and tests on the autoclave cycle itself to verify that the autoclave performs as intended throughout the anticipated operating ranges. Test criteria should match those defined within the User Requirement Specification (URS) document and need to be outlined as part of a pre-approved protocol signed off by your quality assurance team. The tests listed here are ‘suggested’ because the tests you choose will be dependent on your autoclaves application, for example some of the tests are more commonly used in hospitals, whereas others are performed in dental practices. It is also recommended as part of the OQ or the PQ to conduct some steam quality testing which tests your steam supply for non-condensable gases, dryness and super-heat. All of which can impede sterilisation. For all technical testing, we recommend carrying out the tests in triplicate, to reduce the probability that the results obtained occurred by random chance. This approach is also favoured by regulatory bodies.
Initial Checks include:
- Verification that the equipment used in the validation has calibration certificates that are in date
- Alarm Checks
- Cycle tests
- Ensuring SOPs and Operating training is in draft
- Ensuring autoclave is incorporated into the site maintenance schedule
Suggested Tests can include:
- Small Load Thermometric Test
- Full Load Thermometric Test
- Hollow Load Test
- Bowie Dick Test
- Leak Rate Test
- Air Detector Tests (if air detectors are fitted)
a) Small Load
b) Full Load
c) Function
- Load dryness tests
- Small Load
- Full Load, textiles
Tests 1, 4, 5, 6a, 6c and 7b are described below in further detail as these are most commonly performed within the pharmaceutical and medical device manufacturing industries.
Small Load Thermometric Test
This test is designed to challenge the air removal phase of the autoclave, which is the first phase of the cycle in which the vacuum pump removes air from the chamber so it is below atmospheric pressure and following this, steam is added in a series of pulses, to remove the remaining air.
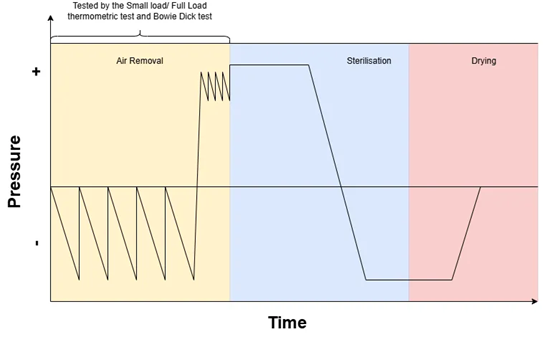
To challenge this phase, it is recommended to assemble a standard test pack (as outlined in section 23.1 of BS EN285). Six temperature sensors are to be placed within the test pack at defined intervals specified in section 16.1.3.6 and one temperature sensor should be placed at a reference point (in the chamber drain). Standard test packs are a common feature of nearly all the tests in the Operational Qualification except the hollow load test.
From the data generated by the seven temperature sensors. There are six key acceptance criteria which must be assessed:
- Equilibration time
- Temperature difference between the drain and aerial sensors within the first 60s
- Temperature difference between the drain, aerial sensors during the plateau period
- Temperature within the drain, test pack and the theoretical temperature of steam during the hold time compared to the sterilisation temperature band
- Temperature difference within the drain, test pack and the theoretical temperature of steam during the hold time
- Sterilisation time
Acceptance criteria tables can be found in BS EN 285
Bowie Dick Test
The Bowie Dick test is a test designed to challenge the air removal phase of the autoclave and is done in conjunction with the small and full load thermometric test. We recently wrote an article dedicated solely to Bowie dick testing here. So if you are interested in learning more about this area, we’d recommend you check it out. Bowie dick test sheets contain a class 2 chemical indicator in accordance with EN ISO 11140-3, ISO 11140-4 and ISO 11140-5. Where successful air removal is demonstrated, a uniform colour change will be observed. No change or partial colour change indicates a failure on this test and further thermometric testing must be initiated to determine the underlying cause. Any pre-vacuum autoclave should not be used until the underlying cause is determined and the necessary corrective and/or preventative action is taken. The test should then be repeated with a passing result before usage can recommence.
Air leakage (also known as a Leak Rate Test)
This test is designed to test the chamber’s leak integrity by pulling a vacuum for 10 minutes and observing any pressure rise, as these signify air leakage. Air leakage into the chamber can impede the penetration of steam into the load, impacting sterilisation. You will need a pressure measuring instrument to observe the pressure within the chamber over time. The test involves first carrying out an operating cycle to warm up the chamber followed by pulling a vacuum for 10 minutes. Once the absolute pressure in the sterilizer chamber is 7 kPa all the valves connected to the sterilizer chamber should be closed and the vacuum pump should be stopped. The pressure in the chamber should then be observed after 300s. The rate of pressure change that can be considered acceptable is equal to or less than 1.3 mbar/min.
Air detector setup and testing (if fitted)
If air detectors are to be fitted, then the height of the air detector must be recorded and justified as part of the Operational Qualification (OQ) testing. Air detectors are commonly set up within cycle development but there are tests you can use to verify the correct placement of air detectors, these are the small load, full load and air detector function tests.
Small Load Test for Air Detectors
This test is designed to determine the rate of induced air leakage that will cause a temperature depression of greater than 2°C inside a standard EN285 test pack (described in section 23.1 of BS EN285). This rate when determined will be used to test the air detector function in the air detector function test. For this test, you will need an induced leak rate valve (to induce the leak to the desired depression), pressure sensors, and a standard EN 285 test pack with five temperature sensors placed inside and one in the chamber drain. You will also need to make sure that the air detectors are turned off. The rate of air leakage should be slowly increased until a temperature depression of 2°C is observed. This rate should be recorded ready to be used in the function test.
Function test for Air Detectors
The air detector function test is used to demonstrate that the air detectors are set up properly and the cycle will successfully abort if a leak is detected. For this test, there are no pressure and temperature sensors needed, just an induced leak valve and a standard test pack. Before performing this test it is important to ensure that a warm-up cycle has been performed, along with a bowie dick and the air detectors are turned on. Prior to this, you also need to ensure the induced leak has been set up at the correct level, by performing either the small or full load test for air detectors.
For the test, you will need to place the standard EN285 test pack in the horizontal centre of the chamber, approximately 100-200 mm above the chamber floor. Once the leak is induced and the cycle is running, you will need to record whether or not the air detector has failed the cycle at the check phase and the cycle is aborted. If this doesn’t happen, this should be accounted as a failure and further development and investigation should be carried out to ensure the air detectors are placed correctly.
Load dryness test, small load, textiles.
The Load dryness test is used to provide a benchmark in which to measure and identify issues with wet loads. It can also be useful in developing new cycles. For this test, you will need a standard EN285 test pack, which will need to be weighed before the test. After placing the load in the horizontal centre of the chamber (approximately 100-200mm above the chamber floor) run a cycle immediately. After 120s of the cycle completing weigh the test pack again and calculate % weight gain. For the test to pass, the mass of the test pack should not increase by more than 1%.
Conclusion
Installation and Operational Qualification form a vital component of testing new autoclaves used within manufacturing pharmaceuticals and medical devices. Following the successful completion of OQ testing and a pass at all stages, you can then move onto Performance Qualification testing which involves tests with the product or qualified substitutes under normal operating conditions with worst-case batch sizes and conditions. It is only then when Standard Operating Procedures (SOPs) can be finalised and operator training conducted.
Further Reading
BS EN 285-Large steam sterilizers. https://knowledge.bsigroup.com/products/sterilization-steam-sterilizers-large-sterilizers-3
Six Common Challenges in Validating Autoclaves